Understanding the Importance of Foam Control in Food and Drink Handling
Understanding the Importance of Foam Control in Food and Drink Handling
Blog Article
A Comprehensive Overview to Implementing Foam Control Solutions in Your Procedures
Effective foam control is a vital facet of operational efficiency that frequently goes ignored. Understanding the complexities of foam generation can significantly affect both performance and product high quality. This overview details the different difficulties postured by foam and the varied options offered, offering a structure for choose and applying one of the most ideal strategies. By analyzing key factors such as application compatibility and workers training, companies can optimize their foam administration initiatives. As we explore these components, the possibility for transformative enhancements in your procedures ends up being evident. What steps will you take following?
Understanding Foam Difficulties
Foam difficulties are a considerable concern across different industries, influencing functional effectiveness and product top quality. The development of too much foam can hinder processes such as blending, transport, and storage space, leading to raised downtime and waste. In fields like food and drink, drugs, and petrochemicals, foam can hinder manufacturing lines, triggering product inconsistencies and contamination risks.
In addition, foam can obstruct equipment functionality, resulting in costly repairs and maintenance. As an example, in wastewater treatment, foam can interrupt clarifier procedures, leading to lower treatment efficiency and governing conformity problems.
Recognizing the underlying causes of foam generation is critical for reliable management. Aspects such as surfactants, temperature level changes, and anxiety levels can all contribute to foam production. Determining these aspects permits sectors to apply targeted methods that reduce foam formation while preserving item stability.
Kinds of Foam Control Solutions
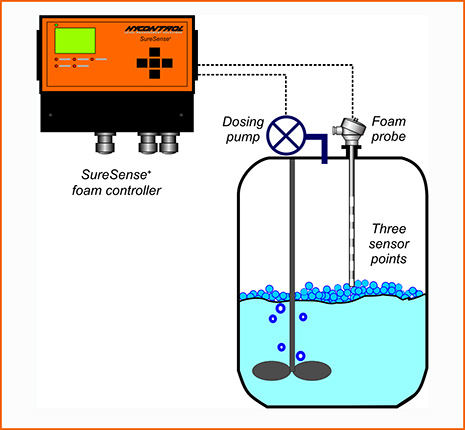
Mechanical options include using tools such as foam skimmers or defoamers. These devices physically get rid of foam from the surface of liquids, consequently protecting against overflow and maintaining optimum levels in tanks and activators. Chemical options, on the other hand, consist of the application of defoaming representatives-- compounds that interrupt the foam framework, resulting in its collapse. These representatives can be silicone-based, natural, or liquid, each offering distinctive advantages depending on the application setting.
Finally, operational techniques concentrate on process changes. This may entail changing equipment criteria, such as temperature and stress, or transforming the circulation rates of liquids to minimize foam generation. Furthermore, applying excellent housekeeping techniques can also minimize foam development by reducing pollutants that add to foam stability.
Picking the proper foam control service entails examining the details demands of the operation, consisting of the kind of procedure, the attributes of the products involved, and security factors to consider.
Choosing the Right Products
Choosing the ideal foam control items needs an extensive understanding of the particular application and its one-of-a-kind obstacles. Elements such as the sort of foam, the atmosphere in which it occurs, and the wanted end result all play essential roles in item option. Foam Control. For example, in markets like food processing, it is imperative to pick food-grade defoamers that adhere to safety and security guidelines while efficiently managing foam.
In addition, take into consideration the viscosity of the liquid where the foam problem exists. Some items are developed for low-viscosity applications, while others are customized for thicker fluids. Compatibility with existing processes is an additional essential element; the picked foam control representatives need to integrate effortlessly without interfering with overall operations.
An additional important factor is the approach of application. Some products may need dilution, while others can be used straight. Evaluating the convenience of usage and the called for dose can provide insights into the product's efficiency and cost-effectiveness.
Application Techniques
Successful application methods for foam control services call for a systematic approach that aligns item choice with operational requirements. The very first action entails a thorough evaluation of the processes where foam takes place, recognizing particular areas that necessitate intervention. By involving cross-functional groups, including engineering, production, and top quality guarantee, organizations can collect insights that inform the selection of the most efficient foam control items.
Next, it is essential to develop clear objectives for foam reduction, ensuring that these goals are measurable and attainable. This may involve specifying acceptable foam levels and the timelines for execution. Educating workers on the properties and application techniques of picked foam control agents is equally vital, as proper usage is essential for ideal outcomes.
In addition, incorporating foam control solutions into existing process needs careful planning. Organizations must establish Click This Link a phased execution strategy, enabling modifications based upon first results. Routine interaction and responses loops with team entailed in the procedure will certainly facilitate prompt analytical and promote a culture of continual renovation. Inevitably, a well-structured technique will boost operational efficiency while efficiently managing foam-related difficulties.
Monitoring and Reviewing Effectiveness
Monitoring and examining the performance of foam control solutions is crucial for making sure that implemented strategies generate the desired results. This procedure involves organized data collection and analysis to More Help analyze the efficiency of foam control representatives and methods. Secret efficiency indicators (KPIs) ought to be established before implementation, enabling for a clear baseline against which to gauge development.
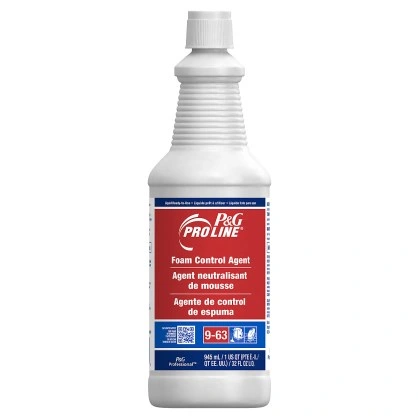
Evaluating efficiency likewise needs routine evaluations of foam control treatments and agent effectiveness. This can be accomplished with tasting and testing, enabling operators to identify if present solutions are fulfilling operational requirements. Additionally, it is critical to obtain feedback from employee who connect with these systems daily, as their understandings can expose operational nuances that measurable information might ignore.
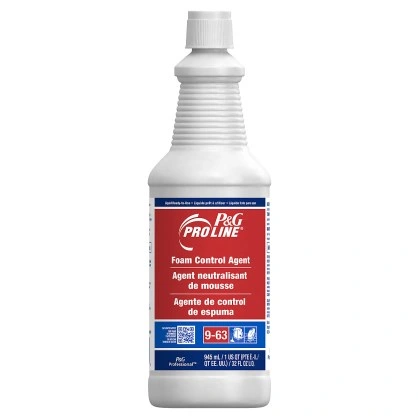
Inevitably, a structured tracking and examination framework aids identify needed adjustments, ensuring that foam control solutions stay reliable, cost-effective, and straightened with organizational goals.
Conclusion
In verdict, effective foam control services are necessary for optimizing functional pop over to this web-site efficiency and maintaining item top quality. An extensive understanding of foam difficulties, combined with the option of appropriate items and application techniques, helps with the effective management of foam generation.
Carrying out great housekeeping techniques can also minimize foam formation by lowering pollutants that add to foam security.
Selecting the right foam control products needs a thorough understanding of the specific application and its distinct obstacles (Foam Control).Successful application approaches for foam control remedies call for a methodical strategy that lines up item choice with functional demands.In conclusion, reliable foam control options are essential for maximizing operational efficiency and preserving item quality. A complete understanding of foam challenges, combined with the choice of ideal products and application techniques, assists in the successful management of foam generation
Report this page